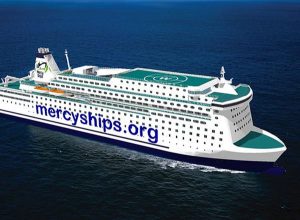
Marine Wastewater Treatment Reaches Municipal Standards
Wastewater treatment aboard maritime vessels can now match land-based processes in purification. And regulations effective in 2016 make it a more relevant topic than ever.
The technology to recover 99 percent of wastewater as reusable has been around for decades, but until recently it’s been confined to land. “The technology itself isn’t new,” says Mats Riska, Product Manager with thecleantech company Evac, headquartered in Finland. “What we figured out is how to build the equipment and take the process to sea.”
According to Riska, 1990s technology – still in use by some – means macerating and adding chlorine, which disinfects but does not decrease the volume of actual waste. In the early 2000s, biological wastewater treatment plants emerged but were often unreliable. Now, the technology has matured, been tested, and is able to produce sufficient effluent quality.
Evac’s MBR (Membrane Bio Reactor) system is commonly found on small cruise ships, ferries, offshore platforms, and other vessels with a large number of people on board. It has recently garnered attention for being selected for use aboard the hospital ship Atlantic Mercy. Owned and operated by the non-profit Mercy Ships, the ship will provide medical care in the poorest parts of Africa. The vessel, now being constructed by the China Shipbuilding Industry Corporation at the Tianjin Xingang Shipyard, will carry as many as 950 patients and crew, who will generate approximately 250 cubic meters of wastewater per day.
The MBR system removes solids, organic material and pathogens from wastewater – recovering 99 percent of the original liquid amount. The biomass grows during this process, and the one percent is separated as excess bio-sludge to be dried and burned. “Atlantic Mercy won’t have to pump anything in port,” says Riska.
Technically speaking
Wastewater purification has two targets, according to Riska. “First, we remove organic material measured as chemical oxygen demand (COD) and biological oxygen demand (BOD), as well as solids and pathogens. Second, we remove nutrients like nitrogen and phosphorous.”
Evac’sMBR system is installed in the engine room with a very minimalfootprint. The actual MBR units are about two-by-five meters, about half the space a traditional Conventional Activated Sludge (CAS) system requires.
The first stage of the MBR systemseparates grease, large particles, and solids in a separate mechanical pre-treatment process. In the second phase,dedicated microbes turn dissolved organic material into carbon dioxide and excess bio-sludge through a biological process.
Membrane filters submerged in the biomassensure that no solids or microbes escape from the system. The pore size of the membranes is so small that no additional disinfection is needed.Finally, the waste streams from mechanical pre-treatment and the excess bio-sludge are then incinerated.
Aboard the Mercy
The Atlantic Mercy, at 174 meters and 37,000 gross tons, will use two MBR reactors. Water will be pretreated to remove large solids (“large” defined as anything bigger than one millimeter). Galley water will go separately through a flotation grease separator. Hospital water will be pre-treated, and a separate sterilizer will service the ship’s intensive care unit.
The Mercy’s two MBR units have submerged membranes in the biomass inside the tank. Microbes do the hard work and only clean water is sucked through the membrane. The pore size of the membranes is so small that even bacteria are removed.
Versus old technologies like CAS, which are employed on most old vessels, Evac’s MBR units have smaller footprints andup to 50 percent space savings is possible. On vessels like the Atlantic Mercy, where 7,000 square meters of deck space are allotted to the hospital alone, space gains matter.
Additionally, by avoiding continuous chemical consumption, running costs are reduced, allowing the operator more resources to devote to its main mission. Evac’s total waste management package’s incinerator andequipment for dry waste handling will mean frequency of trips to shore for waste disposal may be decreased, and environmental impact of waste disposal reduced.
New build versus retrofit
Riska says that MBR technology makes sense for all type of vessels carrying passengers and crew but Evac uses also alternative MBBR (Moving Bed Biofilm Reactor) technology on the biggest cruise ships, where thousands of people generate over a thousand tons or thousand cubic meters of wastewater on a daily basis.
Most of Evac’s sales are new builds, but as regulations tighten retrofits are becoming a bigger business. “For doing a retrofit you need the same skills as you do with a new build, but also a lot of extra layout and mechanical skills,” says Riska. The bulk of the retrofit must be done when the ship is in dry dock, a period of only a couple of weeks.
“It’s important to select a good retrofit partner,” cautions Riska. “Retrofit jobs are very hard to budget, because there can be so many surprises. You might discover thedeck isn’t level under the old equipment. Lots of things can happen and some companies have suffered huge economic losses during a retrofit.”
The letter of the law
Generally speaking, new regulations don’t make demands on old ships. But new regulations effective 2019 will require passenger vessels in Special Areas to improve their wastewater quality. “BOD, COD, solids and bacteria will have to be removed in all areas,” says Riska. “But in Special Areas, currently defined as the Baltic Sea, vessels will be required to remove nitrogen and phosphorous, together referred to as nutrients.”
Test results prove the quality of treated water after Evac MBR significantly exceeds minimum requirements defined by the new IMO MARPOL MEPC.227(64), and vessels equipped with the Evac MBR may be operated in many Environmentally Sensitive Sea Areas and Special Areas defined nationally or internationally, where special discharge restrictions apply.
Riska cautions that the new regulations are written so that new bodies of water may be classified as Special Areas without writing entirely new regulations. New regulations come into effect in 2019 for new ships, and will apply to all passenger vessels in 2021. This means retrofits will be required for some vessels.
Reduced to one percent
While legal regulations will undoubtedly motivate some vessel owners to consider MBR technology, ecological and economic reasons are becoming more persuasive.
“A big vessel with passengers generates thousands of kilograms of waste, thousands of tons of wastewater every single day,” says Riska. Indeed, a cruise vessel with around 1,500 passengers generates 500 tons of wastewater per day, roughly enough to fill a large, single-family home.
“But with our technology,” adds Riska, “it can be reduced to a little over one percent of its original size and weight. The savings in disposal costs are not only impressive, but it’s also quite a win for the environment.”
